EAGLE EYE
TOP COAT
INSPECTION
Autonomous machine vision inspection system for the detection of defects on painted vehicle body surfaces
AN INNOVATIVE SYSTEM THAT STANDS OUT FOR NOT HAVING TO STOP BODIES DURING THE INSPECTION PROCESS
The Eagle Eye – TCI was first installed in 2014 on a vehicle production line, standing out for not having to stop the bodies during the inspection process or having to remove the body from the production line, in addition to being a system without moving parts.
The Eagle Eye – TCI systems is controlled by a single PC, which is responsible for the treatment, calculation and control of the installation. Making its maintenance minimal and very easy to integrate with the cybersecurity of the plant.
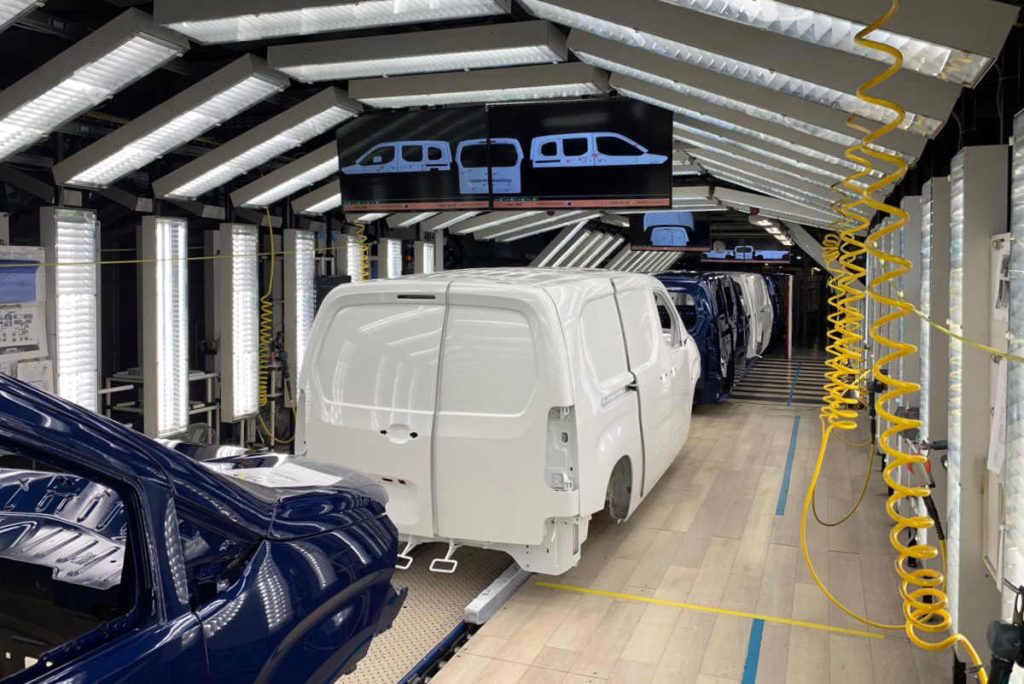
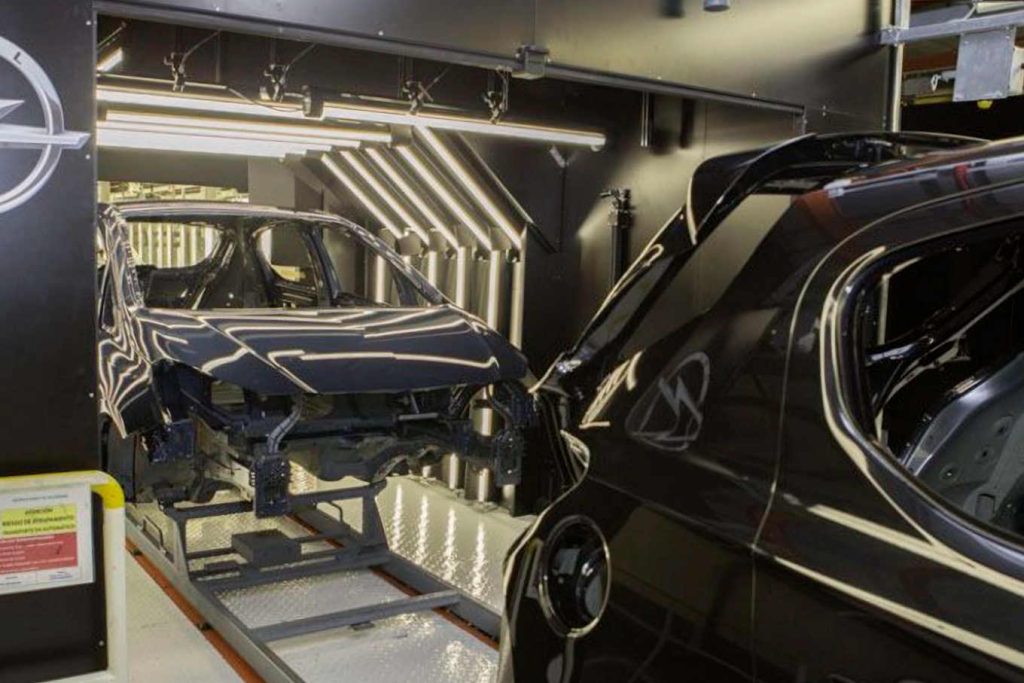
WITHOUT STOPPING, REGISTERING IN A FIXED POSITION OR REDUCING THEIR SPEED
The Eagle Eye – TCI system is designed to have the minimum interference with the productive system of the plant. During the inspection it is not necessary for the bodies to stop, register to a fixed position or slow down their speed.
The system also allows the simultaneous inspection of two consecutive bodies, it is not necessary that the inspection of the first one has finished for the inspection of the second to start. In addition, the inspection process adapts to the normal work flow of the line, allowing stops and starts during the inspection, and changes in the line speed.
A FULLY ADAPTABLE SYSTEM
Each Eagle Eye – TCI is specifically designed for the bodies that are manufactured in each plant, having approximate average dimensions of 3.5m (wide) x 4.3m (large) x 3m (height) for the inspection of commercial vehicles, being able to change these dimensions to adapt to the inspection of other types of vehicles.
The design is also adjusted for the maximum speed of the bodies in the inspection zone, allowing subsequent changes in line speed as long as the maximum design speed is not exceeded.
The Eagle Eye – TCI system has a standard speed of 10-15 m/min (up to 150 jph), but it can be adjusted to higher speeds, expanding its capabilities. After the Each Eagle Eye – TCI is installed and calibrated the system already has a high level of defect detection, with the final start-up and adjustment time being around 10 weeks after calibration.
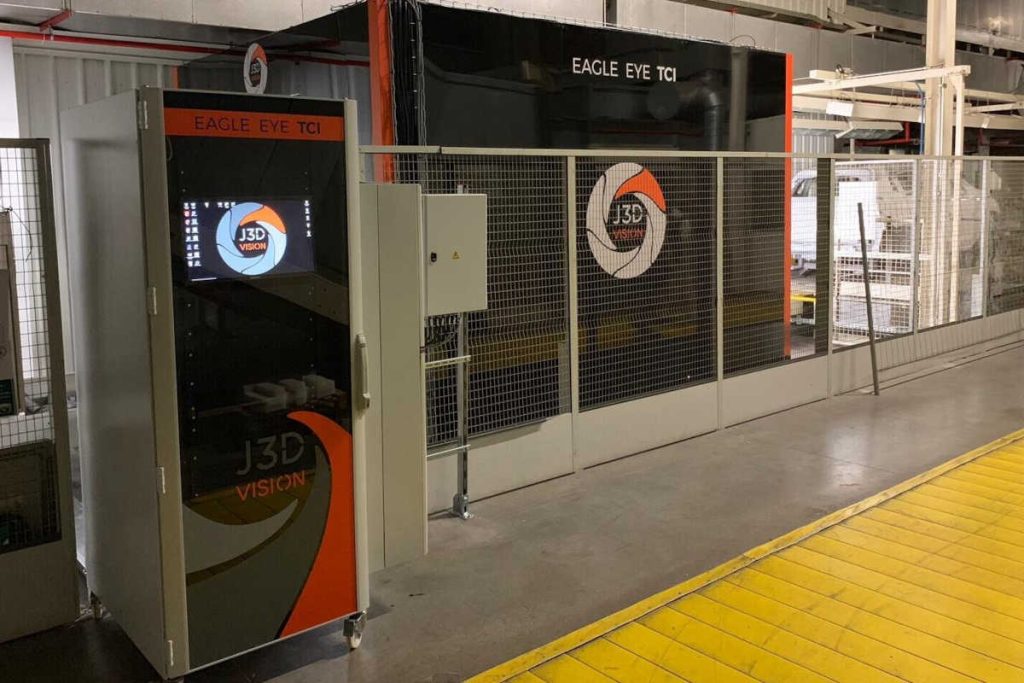
THE EAGLE EYE – TCI SYSTEM GENERAL CHARACTERISTICS
Detection and classification of all types of defects: orange peel, dirt, dents, drops, peeling paint, scratches, sandingmarks, uncovered surface…
Detection of defects in edges and characteristic lines.
Detection sensitivity adjustable by model, color, zones and other parameters.
Full surface aspect measurement. Advanced optical aspect measurement algorithms correlated with traditional aspect parameters.
Two methods of filtering defects: by sizeand by statistical severity. Smart filtering rules by area and easy adjustment of filters from raw data.
Two-tone vehicle inspection in asingle pass or in parts according to plant needs.
Inspection of out of position parts attached to the body: fuel caps, metallic windows…
Adaptation to new car models and new colors, easy adjustment of new colors or special colors (fleets) from the initial color calibration.
Statistical analysis module and results reports and traceability of inspection results. Generation of statistical reports in a dedicated module according to plant needs. Inspection results stored in a database for consultation and analysis.
General interface and operator interfaces. Configurable on-line display and control interface at each repair station. Possibility of printed results chart.
Design becomes adaptability
The Eagle Eye – TCI features a modular design that allows the inspection tunnel to integrate seamlessly with any plant layout.
This means that no modifications to the existing line or conveyor system will be necessary when installing the Eagle Eye – TCI, saving time and money.
The inspection tunnel can be installed anywhere on the production line before the finishing area.
This allows the Eagle Eye – TCI system to be installed as a continuous configuration.
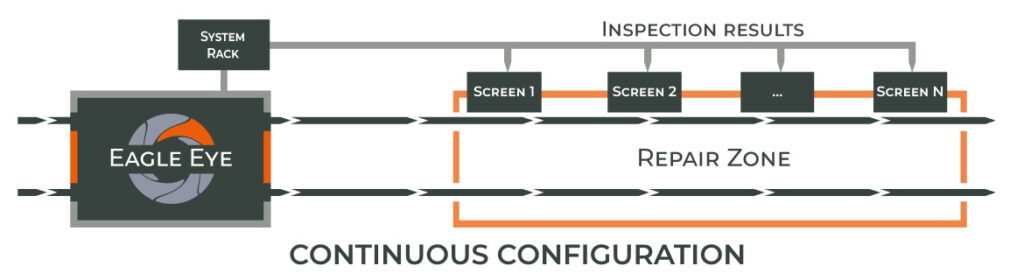
In addition, the Eagle Eye – TCI system can be configured as a split configuration instead of continuous. This means that the system can be split into separate parts for more efficient operation and maintenance.

The Eagle Eye – TCI system offers more than just a single or split configuration. In fact, it is versatile enough to serve multiple finesse lines.
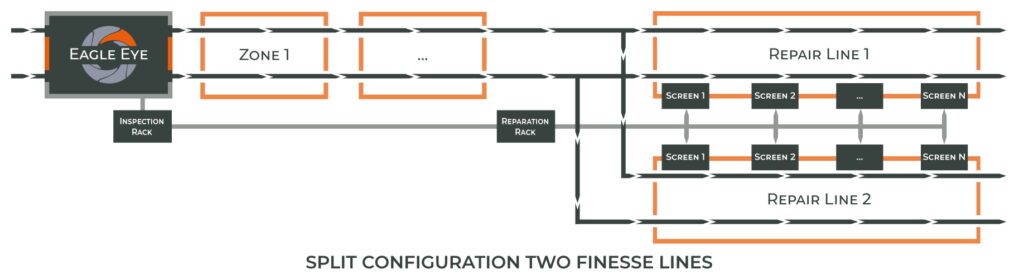
Want to know more?
Ask us today!
The development of highly specialised systems in precision engineering and precision measuring techniques with and without contact is our core business.